품질에 관련된 문제의 대부분은 품질특성의 설계단계부터 내재 적극적 의미에서의 품질향상을 위한 노력은 효율적인 설계에서부터 시작되어야 함
기존의 관리도기법은 이미 설계된 품질을 갖는 제품의 제조공정에서 발생할 수 있는 공정이상상태를 사전에 감지하여 예방
공정의 분산을 근본적으로 감소시키거나 품질을 개선시키지는 못함
다구찌 기법은 설계단계에서의 품질 중요성을 강조하는 실용적인 방법론
기존의 관리도 중심의 통계적 공정관리기법 (online QC), 다구찌 기법 (offline QC) 두 개를 합쳐서 품질공학(quality engineering)이라고 부르기도 함
12.1 다구찌의 품질해석 및 손실함수
일반적으로 품질이란 사용의 적합성(fitness for use) 또는 목적의 적합성(fitness for purpose) 로 정의
다구찌는 여기에 품질손실 개념을 도입하여 '제품이 출하된 시점으로부터 성능특성치의 변동과 부작용 등으로 인하여 사회에 끼친 손실' 이라는 개념으로 품질을 정의
여기서 사회에 끼친 손실이란 어떤 제품의 품질특성이 목표치를 벗어남으로써 발생하는 손실을 화폐가치로 환산한 양
크게 생산자 손실과 소비자 손실을 합한 것으로 볼 수 있음
기존 개념 - 어떤 품질특성이 규격 또는 허용차의 한계 내에만 있으면 양품으로 간주되었고 어떤 손실도 발생하지 않는 것으로 여겨짐 (규격의 상한선 또는 하한선을 넘을 때 손실 발생)
다구찌 - 품질특성치가 소비자 규격 내에 부합된다고 하더라도 목표치에서 벗어남에 따라 어느 정도의 손실이 발생
기존 품질 개념에 의한 손실함수와 다구찌 손실 함수
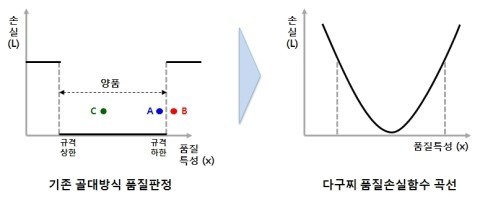
품질특성치가 소비자 규격 내에 든다 하더라도 목표치에서 벗어남에 따라 포물선 모양의 손실이 발생한다고 주장
따라서 동일한 공정 품질과 규격하에서 다구찌 개념에 의한 손실비용이 기존 개념의 손실비용에 비해 더 크게 해석되므로 생산자의 품질편차를 줄이려는 노력을 유발
기존 손실함수의 모순점은 품질특성치가 규격 하한선에 겨우 들어온 경우 아무론 손실이 없다고 보지만 약간 벗어난 경우에는 급격하게 손실비용이 발생함
이에 반해 다구찌 손실함수는 품질특성치가 목표치에서 벗어남에 따라 손실비용이 부드러운 곡선 형태를 가지며 증가 실제와는 다를 수 있지만 이 방법이 단순하면서도 합리적인 것으로 평가됨
품질에 따른 다구찌의 손실함수를 타당한 것으로 여기는 생산자라면 품질 손실을 줄이기 위해 품질특성을 될 수 있으면 목표치에 가깝게 하려고 노력
이에 반해 기존의 손실함수를 믿는 생산자는 품질을 목표치와는 무관하게 규격 내에 들도록 하는 것에만 관심
일반적으로 품질특성치의 종류는 다음과 같이 세 가지로 분류
- 품질특성치가 목표치에 가까울수록 좋은 경우 (nominal-the-best characteristic)
품질특성치에 특정한 목표치가 주어져 있고 품질이 목표치에 가까울수록 좋은 경우 (망목특성)
측정치가 y이고 목표치가 m인 경우에 손실함수 를 다음과 같이 정의할 수 있음
이 함수는 y에 대한 연속함수로써 2차 곡선으로 나타낼 수 있음
상수 k는 손실을 화폐가치로 환산할 떄 적절하게 산정 가능 예를 들어 위 그림과 같이 규격이 인 품질특성치가 규격 끝에 닿을 때 비용 C가 발생한다면 의 관계에 의해 로 구할 수 있음
- 품질특성치가 작을수록 좋은 경우 (smaller-the-better characteristic)
진동, 불량률 등 특성치가 작을수록 좋은 경우(망소특성)
일반적으로 목표치 m은 0이므로 손실함수는 식 12.1로부터 아래와 같이 나타낼 수 있음
- 품질특성치가 클수록 좋은 경우 (larger-the-better characteristic)
수명, 수율, 적중률 등과 같이 특성치가 클수록 좋은 경우 (망대특성)
특성치 y를 변환시켜 로 하면 는 망소특성의 성질을 가지게 되므로 식 12.2에 대입가능
포물선 모양을 가지는 망목특성의 경우 품질특성치를 (어떤 값을 가질지 모르는 확률변수)로 표기하면 다음과 같이 손실함수를 표기할 수 있음
이 경우 손실을 줄이는 문제를 이론적으로 생각해보면 역시 확률변수이므로 이의 기대치를 구하면 다음과 같음
즉, 기대손실은 Y의 분산, 그리고 Y의 평균과 목표치와의 편차로 구성되므로 품질특성치의 평균이 목표치와 일치한다면 기대손실을 줄이기 위해서는 공정의 분산 또는 표준편차를 줄여야 함
식 12.4의 기대손실은 망소특성의 경우에도 m=0으로 하면 동일하게 적용 가능
12.2 다구찌의 품질설계
일반적으로 제품개발이 이루어지는 순서는 제품설계, 공정설계, 제조의 세 단계로 나뉘고 각 단계는 다시 여러 세부단계로 이루어짐
어떤 한 단계의 산출물(output)은 바로 다음 단계의 입력(input)으로 투입되므로 모든 단계가 서로 연결되어 있으며 위의 세 단계 모두가 제품의 품질 및 원가에 영향을 줌
그러나 제품의 특성이 점차 복잡해짐에 따라 제품설계 및 공정설계의 중요성이 높아지고 있음
제품설계의 중요성은 주위에서 흔히 경험하는 제품설계상의 결함에 의한 사용상의 불편함 등으로 이해 가능
일반적으로 제품의 실제 성능은 사용되는 환경요인, 제품의 시간에 따른 노후, 공정상의 변동 등에 의해 다르게 나타남
이러한 환경요인에 의한 성능의 차이, 혹은 변동을 없애기 위한 수단이 표 12.1에서와 같이 제품설계단계에서는 가능하나 공정설계 혹은 제조단계에서는 이미 불가능
이에 비해 공정상의 변동에 의한 성능의 차이는 모든 단계에서 제거 가능
<표 12.1>

제조공정에 있어 공정설계에 따라 불량률도 좌우될 수 있음 그리고 주어진 공정설계에서 공정관리를 철저히 할수록 제조상 불량률을 감소시킬 수 있으나 이를 위해선 많은 비용이 필요
따라서 불량률도 줄이면서 공정관리비용 역시 감소시키려는 노력이 필요 공정설계의 향상이 한 방법
아래 그림은 공정설계 향상 전후에 대하여 공정관리의 정도에 따른 제조상 불량률을 나타낸 것

즉, 공정설계를 향상시키기 전에는 만큼의 공정관리로서 만큼의 불량률을 내고 있었으나 공정설계의 향상으로 이전보다 적은 의 공정관리로 더욱 낮은 불량률 를 이룩할 수 있음
이와 같은 공정설계 활동은 시스템 설계, 파라미터 설계, 허용차 설계 등을 통하여 체계적으로 이루어져야 함
- 시스템 설계
시스템 설계는 바람직한, 또는 소비자가 요구하는 기본적 기능을 지닌 원형(prototype)을 개발하는 것 소비자의 욕구 및 제조와 관련된 제반 환경요인들을 고려해야 함
- 파라미터 설계
시스템 설계가 이루어진 다음에는 제품의 기능에 있어서의 변동을 최소화시킬 수 있도록 시스템의 각 요소의 요인수준을 결정해야 하는데 이를 파라미터 설계라고 함
목표치를 조정하는 평균조정인자 또는 수단은 통상 있게 마련이므로 공정조건을 정하는데 있어 공정조건과 품질특성치의 비선형성을 활용하여 편차가 적은 수준을 우선적으로 선택해야 함
요인 수가 많아지면 실험계획법에 의해 제품성능을 목표치에 가능하면 가깝게 유지하면서 각종 변동에 의한 형향을 최소로 하는 부품요인의 적정 수준을 찾아낼 수 있음
설계에 관련된 요인은 크게 제어요인(control parameter; 설계요인이라고도 함)과 잡음요인(noise parameter; 잡음)으로 구분
여기서 제어요인이란 생산자에 의해 설정되는 요인을 말하고, 잡음요인은 생산자가 제어할 수 없고 소비자의 사용환경에 따라 변할 수 있는 요인을 말함
잡음요인은 다시 아래 세 가지로 분류
- 외부 잡음요인(outer noise) - 온도, 습도, 압력 등과 같은 외부 사용 환경조건의 변화에 의한 변동
- 내부 잡음요인(inner noise) - 제품을 사용하는 과정에서 발생되는 노후, 혹은 내부 마모나 열화 및 퇴색에 의한 변동
- 제품 잡음요인(product noise) - 제품의 불완전 제조에 의해 발생되는 제품 간 성능특성치의 산포에 따른 변동
파라미터 설계 실험의 목적은 제품성능에 끼치는 잡음요인들의 영향을 최소화시키는 각 설계요인의 수준을 찾아내는 것
실험계획법을 통해 체계적으로 설계요인의 수준을 변화시키고 각 실험에서의 잡음요인의 영향을 비교함으로써 최적수준조합을 도출
여기서의 실험계획은 12.4절의 직교배열표을 사용함 - SN비로 환산한 특성치를 이용
- 허용차 설계
시스템 설계가 완성되고 파리미터 설계를 통해 부품들에 대한 최적수준조합이 얻어지면 허용차 설계를 통해 품질과 비용을 동시에 감안한 적정수준의 허용차를 결정
이를 위해 우선 각 요인수준의 허용가능한 편차를 알 필요가 있음 편차의 범위가 좁을수록 품질은 상승하므로 제품의 원가 및 제조비용이 증대되는 반면에, 편차의 범위가 넓을수록 제품의 기능이 목표치에서 벗어나는 경향이 많아지므로 품질은 떨어지게 됨
따라서 허용차 설계의 목적은 가장 경제적인 허용치를 결정하는 것이며 이를 위해 손실함수의 개념이 사용될 수 있음
12.3 SN 비
다구찌기법에서 각 실험의 특성치로 SN비 이용 이는 원래 통신공학에서 이용되어 온 개념
통신공학에서 기능적인 품질특성을 다룰 때 아래 그림과 같이 신호입력과 잡음이 시스템의 산출물에 어느 정도의 영향을 주는가를 조사함

목적을 수행하기 위해 전달된 신호입력이 산출물의 품질수준에 영향을 주며, 시스템에 가해지는 잡음이 산출물의 품질에 변동을 초래하게 되어 결과에 대한 신뢰성을 떨어뜨리게 됨
SN비는 신호 대 잡음의 비율을 의미하는 것으로 다음과 같이 신호입력의 힘과 잡음이 주는 영향의 힘의 비율로서 나타내어짐
위 식으로 나타내어지는 SN비는 품질특성치의 종류별로 다르게 정의하여 사용되나 어느 종류나 항상 그 값이 클수록 좋은 것으로 해석됨
SN비를 실험데이터로부터 추정할 때 다구찌는 망목특성에 대해서는 아래와 같은 식을 사용
식 12.5는 손실함수와 관계가 있음 망목특성의 경우 식 12.4의 기대손실을 다음과 같이 쓸수도 있음
공정평균 를 배 하여 목표치에 맞출 수 있다고 할 때 이 경우 공정표준편차도 배로 증가한다고 하면 이고 새로운 공정분산은 이 되고 기대손실은 다음과 같다
그러므로 기대손실을 줄이는 것은 을 작게하는 것이고 이는 다시 식 12.5와 같이 을 크게 하는 것
n개의 데이터 에 대해 를 표본평균, 를 표본분산이라 하면 식 12.5에 의해 은 으로, 은 으로 추정되기 때문에 SN비는 다음과 같이 나타낼 수 있다
따라서 평균값이 클수록, 또는 표본분산이 작을수록 SN비는 커짐
그러나 실제 사용되는 SN비의 값은 통신공학에서와 같이 위의 식에 상용대수를 취하고 10을 곱하여 데시벨(db; decibel)의 단위로 나타냄
즉, 망목특성인 경우 SN비는 아래와 같다
식 12.7의 SN비는 n이 상당히 클 경우 을 무시하면 다음과 같이 구할 수도 있다 대부분의 경우 가 보다 크므로 이 그다지 크지 않더라도 이 무시될 수 있다
망목특성의 손실함수를 나타내는 식에는 목표치가 존재하나 SN비 공식에는 목표치가 포함되지 않는 이유는 품질특성치의 평균(\mu)이 목표치와 일치하거나, 평균을 목표치에 맞출 수 있다는 가정이 내포되어 있기 때문임
망소, 망대 특성의 경우에는 각각 식 12.2, 12.3의 손실함수를 바탕으로 다음과 같이 SN비를 정의함
12.4 직교배열표에 의한 실험계획법
파라미터 설계 단계에서 각 설계요인들의 최적수준조합을 찾기 위해서는 체계적인 실험이 수행되어야함
이를 위해 일반적인 실험계획법을 사용할 수 있으나 인자 수와 수준 수의 증가에 따라 필요한 실험 수가 지나치게 많아질 수 있으므로 다꾸찌는 적은 실험 수로 주요한 결과를 얻을 수 있는 직교배열표(orthogonal array)에 의한 실험을 제안
12.4.1 직교배열표
제품의 품질이나 생산성을 향상시키거나 불량률을 감소시키고자 하는 실험에서 일반적으로 고려해야할 인자 수는 매우 많음
인주 수가 많은 경우에 주효과와 기술적으로 보아 있을 것 같은 2인자 교호작용을 우선적으로 검출하고, 과거의 경험 등으로 미루어 보아 없으리라 예상되는 2인자 교호작용 및 3차 이상 고차의 교호작용의 분석은 배제하여 실험횟수를 줄이고자 함
이러한 목적하게 실험계획을 수립할 수 있도록 만들어 놓은 표가 직교배열표
직교배열표는 각 인자의 수준이 2개인 경우와 수준이 3개인 경우가 가장 많이 사용되고 있음
수준이 2개인 직교배열표는 일반적으로 으로 나타내는데 여기서 은 행의 수이자 실험 수를 나타내며, 배치가능한 최대 인자 수, 즉 직교배열표 상에서의 열의 수는 개가 됨
예를 들어 는 4가지의 실험을 하며 3개의 열을 갖고 있는 직교배열표를 의미
수준이 3개인 직교배열표는 일반적으로 으로 나타내는데 이 경우 실험 수가 가지 이며 열의 수는 개
<표 12.2> L4 직교배열표

표 12.2에서 보는 바와 같이 직교배열표에서는 첫 번째 수준을 0으로, 두 번째 수준을 1로 적기로 함
또한 위의 표에서 다음과 같은 직교배열표의 특성을 볼 수 있음
- 모든 열은 서로 직교(orthogonal)하고 있음 (0을 -1로 바꾼 임의의 두 열벡터의 내적은 0)
- 어느 열이나 0과 1이 반반씩 나타나고 있다
- 3열은 1열과 2열을 합한 것으로 2로 나눈 나머지로 만든 것이다
12.4.2 인자배치
직교배열표에 인자를 배치시키는 방법에는 기본표시에 의한 방법과 선점도(linear graphs)에 의한 방법이 있음
- 교호작용이 없는 경우
교호작용이 없다고 판단되는 경우 인자의 주효과만을 분석하려는 것 이 때는 각 인자를 임의의 열에 배치할 수 있음
그러나 모든 열에 인자를 배치한다면 오차를 검출할 수 없으므로 통상 인자의 수가 6개 이하인 경우에 L8표를 이용할 수 있음
- 교호작용이 있는 경우 인자들의 교호작용을 고려하여야 하는 경우 인자수와 고려하는 교호작용을 더한 요인수를 발탕으로 직교배열표를 선정해야함
12.5 파라미터 설계
파라미터 설계를 위한 실험 및 결과분석 과정은 11장의 일반적인 실험계획에서와 거의 동일
- 인자와 인자의 수준을 정함
- 수준수와 요인(인자 및 교호작용)의 수를 고려하여 적절한 직교배열표를 선정
- 직교배열표에 인자(또는 교호작용)를 배치
- 배치된 인자의 실험조건에 따라 실험을 반복적으로 실시하고 결과를 측정
- 각 실험번호에 해당하는 결과치들을 SN비로 환산
- SN비 데이터를 바탕으로 간이분석법, 또는 분산분석법을 통해 결과를 분석
파라미터 설계의 목적은 잡음의 영향 하에서 성능특성치의 분산을 작게 함과 동시에 평균을 목표치에 근접시킬 수 있는 제어인자의 적절한 수준을 찾는 것으로 일반적으로 다음 2가지 과정을 거침
- 실험은 직교배열표를 이용하여 설계되며, 제어인자들에 대한 동일 실험 조건하에서 2번 이상의 실험을 반복
이처럼 반복 데이터를 얻는 것은 성능특성치에 대한 잡음(외부, 내부, 또는 제품간의 잡음)이나 제어하기 어려운 인자의 영향을 오차항으로 간주하고 오차항의 분산을 보다 정확하게 추정하기 위함 잡음을 실험에서 고려할 수 있는 특수한 상황에서는 잡음인자 및 수준을 고려하여 제어인자 실험조건에 결합시키는 경우도 있음
- 분산분석시에 특성치 데이터에 대해 직접 분석하지 않고 이들로부터 계산된 SN비를 계산하여, 이를 새로운 특성치로 삼아 분석을 실시
분산분석이나 간이분석 등을 통해 성능특성치의 평균, 또는 SN비에 유의한 영향을 주는 제어인자를 찾을 수 있는데 전자를 평균조정인자, 후자를 산포제어인자라 부름
만일 하나의 인자가 성능특성치의 평균과 SN비에 동시에 옇양을 준다면 이는 산포제어인자로 분류
파라미터 설계 시 고려해야 할 주요 착안점으로 다음의 네 가지를 들 수 있음
첫째, 품질특성치의 산포를 줄인다
이를 위해 잡음에 최소의 여향을 받는 생산 및 공정조건을 설계함으로써 품질의 안전성을 도모
둘째, 품질특성치의 평균값을 목표치에 근접시킨다
품질특성치의 평균값에 유의한 영향을 미치는 설계요인들을 선택하여 평균값을 목표치에 근접시킬 수 있는 각 요인들의 수준을 결정
그러나 임의의 설계요인에 대해 산포를 최소화시키는 조건이 우선해야 함
셋째, 비용을 최소화시킨다 첫째와 둘째 단계에서 최적수준이 결정되지 않은 요인의 수준은 비용을 작게 하는 수준으로 선택
만약 낮은 등급의 부품이 정해 놓은 허용차를 만족시키지 못하는 경우에는 허용차 설계 단계에서 조사하여 부품을 선별적으로 대체
넷째, 설계요인의 조건들은 실험의 재현성이 있어야만 실질적인 가치를 가지므로, 확인실험을 통해 재현성이 있는 결과가 얻어졌는지 확인
이상의 네 가지 착안점은 주로 품질특성치가 망목특성인 경우에 고려되어야 하며, 망소특성인 경우에는 SN비를 품질특성치로 이용한다면 품질특성치의 평균값이 작아질수록 산포도 따라서 작아지는 성질을 가지고 있기 때문에 첫째와 둘째 단계를 하나로 생각해도 무방
품질특성치가 망대특성인 경우에도 역시 역수를 취하면 망소특성과 동일하게 취급할 수 있으므로, 첫째와 둘째 단계를 합쳐 SN비만을 가지고 설계인자의 조건을 선택
12.5.1 간이분석법
이 절에서는 직교배열표에 근거하여 실험을 실시하고 결과를 SN비로 환산할 경우 이 값들을 바탕으로 간편하게 분석할 수 있는 간이분석법(또는 파레토분석)을 2수준과 3수준 실험으로 구분하여 설명
2 수준 실험에서 간이분석
L8, L16 등과 같이 2수준 직교배열표를 사용하여 실험을 실시하고 SN비를 구하면 표 12.5와 같은 결과를 얻음 여기서 고려하는 요인(인자 및 교호작용) 수를 N이라 하고 각 요인을 으로 나타내며 실험수를 으로 나타냄
<표 12.5>2수준 실험의 SN비
실험번호 | | SN비 |
| 직교배열표(0 또는 1) | |
합계 | |
어떤 요인이 유의하다는 것은 수준 0과 수준 1에서의 평균반응치에 유의차가 있다는 것이므로 간이분석에서는 각 요인에 대해 수준 0일때의 SN비의 합과 수준 1일때의 SN비의 합을 구한 후 이들 차이의 절대값, 즉 범위를 갖고 요인별로 비교
요인 에 대해 수준 0에서의 SN비의 합을 , 수준 1에서의 SN비의 합을 이라 할 때, 요인 에 대한 수준간 범위 는 다음과 같다
그리고 수준간 범위를 요인별로 비교하기 위해 다음과 같은 기여율을 산출
이 기여율을 큰 순서대로 파레토 그림으로 나타내면 요인에 대한 유의정도 또는 중요도를 쉽게 알아볼 수 있음
<표 12.6> 2수준 실험의 간이분석표
| 합계 | ||
SN비 합계 | 수준 0 수준 1 | | |
수준간 범위 | | | |
기여율(%) | | 100 |
3수준 실험에서의 간이분석
L9, L27과 같은 3수준 직교배열표를 사용하여 실험을 실시하고 SN비를 구하면 표 12.5와 같은 결과를 얻음 (단, 여기서는 직교배열표에 0,1,2의 수준이 사용됨)
요인수 및 실험수를 2수준 실험과 동일하게 정의하고 요인 에 대해 각 수준에서의 SN비 합을 다음과 같이 정의
요인별 수준수가 3개이므로 어떤 요인이 유의하다는 것은 두 수준씩 비교할 때 그 차가 크다는 것이므로 다음과 같은 제곱합을 산출
이는 분산분석표에서의 제곱합과는 약간 다르나 유사
따라서 요인 의 기여율은 다음과 같이 산출함
이를 정리하면 표 12.7과 같은 간이분석표를 작성할 수 있음
<표 12.7> 3수준 실험의 간이분석표
| 합계 | ||
SN비 합계 | 수준 0 수준 1 수준 2 | | |
제곱합 | | | |
기여율(%) | | 100 |
12.5.2 분산분석법
간이분석표에 의해 분석이 가능하지만 보다 정식적인 방법으로 분석하고자 할때는 분산분석법 사용
2 수준의 직교배열표에 의한 실험은 요인배치법과 유사하며, 3수준의 직교배열표에 의한 실험은 요인배치법과 유사하므로 그 분석방법도 유사
2 수준 실험에서의 분산분석표
요인 에 대한 제곱합은 다음과 같이 산출됨
위의 식은 수준이 2인 요인배치법의 경우와 유사한 것을 볼 수 있는데 여기서는 실험수가 이기 때문이 M으로 나눔 식 11.23a에서는 실험수가 , 식 11.29a에서는 실험수가 이기 떄문에 각각 이 값들로 나눔
그리고 전체제곱합은 다음으로부터 구할 수 있음
CT는 수정항으로 다음과 같은데 여기서 T는 SN비의 전체합
오차제곱합은 아래와 같음
<표 12.8> 2수준 실험의 분산분석표
요인 | 제곱합 | 자유도 | 평균제곱 | F-값 |
| | | | |
오차 | | | | |
전체 | | |
3 수준 실험의 분산 분석표
2수준의 경우 식 12.14는 다시 다음과 같음을 알 수 있음
이를 3수준 경우로 확장하면 요인 f_i에 대한 제곱합은 다음과 같음을 유추 가능
여기서 CT는 수정항으로 다음과 같다
식 12.18의 제곱합은 다시 아래와 같이 표현됨
전체제곱합은 다음과 같다
오차제곱합은 다음과 같다
<표 12.9> 3 수준 실험의 분산분석표
요인 | 제곱합 | 자유도 | 평균제곱 | F-값 |
| | | | |
오차 | | | | |
전체 | | |
분산분석표로부터 F-검정을 통해 각 요인의 유의성을 검정하며 유의한 인자들에 대해 최적수준조합, 즉 최적조건을 구할 수 있음
SN비를 데이터로 사용하기 때문에 평균반응치가 가장 큰 조건들을 산출하면 됨
Uploaded by N2T
'기초지식' 카테고리의 다른 글
13장. 통계적 품질관리 (1) | 2023.07.24 |
---|---|
11장. 실험계획법 (1) | 2023.06.06 |
10장. 특수회귀모형 (0) | 2023.06.06 |
9장. 다중회귀분석 (0) | 2023.06.06 |
8장. 단순회귀분석 (0) | 2023.06.06 |